UP Catalyst is now one step closer to upscaling its production and securing the European supply chain for sustainable carbon nanomaterials and graphite. The first automated shipping container, able to transform 10 tons of CO2 and produce 2.7 tons of carbon material, is reaching the end of its design phase, with its construction expected to conclude by Q1 2023.
The implementation of the revolutionary project named “CO2Carbon” aims to disrupt the carbon material production chain for EV batteries. The project with a budget of €1.59 M received funding from EIT RawMaterials to design and construct an automated container for producing carbon materials directly from CO2. The utilization of CO2 to produce the much-needed graphite for the automotive industry presents a unique opportunity to manufacture truly sustainable batteries.
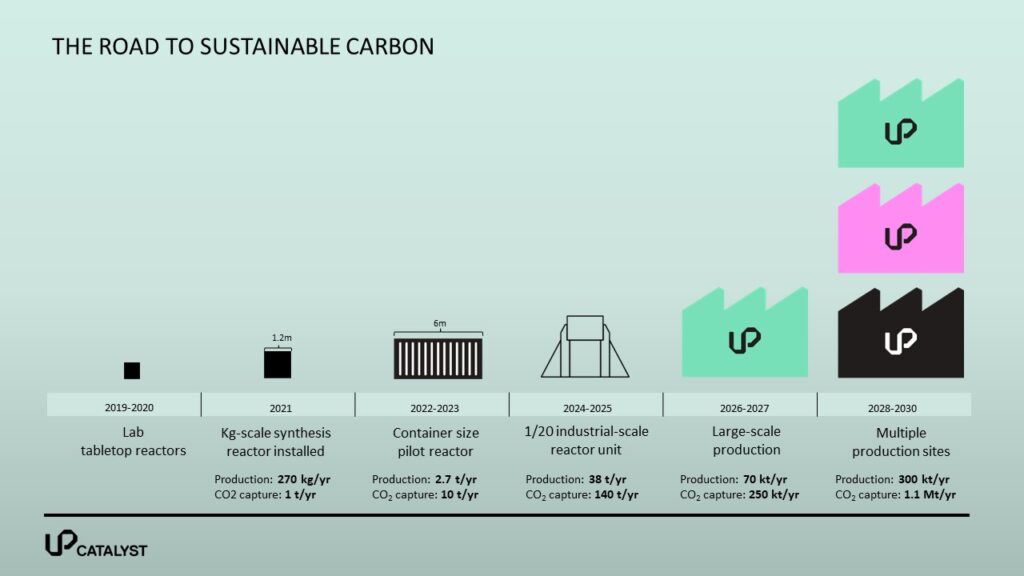
Why is carbon important and how is it currently produced?
Carbon is a versatile element that can be found everywhere around us in different shapes and forms. Carbon materials are important components in the gadgets you are using daily, as well as in the vehicles you take to get to work. Carbon is present in all living things on Earth, and yet its industrial production for commercial applications has taken a toll on the environment.
In nature, pure elemental carbon occurs in two forms: diamond and graphite. As a raw material, graphite has sparked lots of interest due to its use in the anodes of electric vehicle batteries – an average EV battery contains around 56 kg of carbon. The explosion in carbon demand is expected to reach 10 Mt by 2030, driven by the rapid growth of the EV industry. Until now, the valuable mineral for energy storage solutions has been either mined or synthesized from fossil fuel-based resources.
Synthetic graphite production requires fossil-based raw materials, such as petroleum coke, coal-tar pitch, or oil, to be heated at high temperatures. The use of toxic chemicals has a huge impact on the environment. In fact, for every ton of synthetic graphite produced 13.8 tons of CO2 is emitted into the atmosphere. This method is not energy efficient and contributes to air and water pollution.
The other alternative, natural graphite, is believed to be a greener choice as its production is less energy-intensive. But what is the reality? Depleting the Earth’s natural resources by mining to extract the enormous amounts of graphite needed does not align with the world’s sustainability goals. Furthermore, the lifecycle analysis for natural graphite mining and processing raises concerns, as documented by an LCA conducted for a representative Chinese graphite manufacturer. Starting from graphite mining up to the final stage of purification, the total energy demand is assessed as 31.25 MWh/ton and the carbon footprint is estimated at 5.3 tons CO2-eq/ton graphite.
At the same time, there are indirect environmental and societal impacts of graphite mining that one should take into account. Graphite mining causes enormous amounts of dust resulting in air pollution. In addition to the harmful waste created, there are minerals inside graphite that can cause acid mine drainage, when exposed to water or air, and consequently, put all life in the local ecosystem at risk. The lack of clean water and air near mining sites leads to biodiversity loss and an increase in health problems for the local population.
CO2Carbon: a European vision for green batteries
Cutting down emissions and decreasing fossil fuel use has been the primary reason for the automotive industry to shift to electric vehicles. But the huge environmental cost of EV battery production puts the entire premise of sustainability into question. CO2Carbon brings together distinguished academic and industrial partners from all around Europe to make the green battery vision a reality.
It is the first scalable technology in the world to produce sustainable carbon for the EV industry in a process, where CO2 is sequestered as a feedstock into the valuable carbon raw materials, rather than released. The completion of the design and the construction phase marks a new era in the production of carbon nanomaterials and graphite. UP Catalyst has developed a technology that is easily scalable, thus can cover the market’s demand for graphite and can offer high-purity carbon ideal for battery applications with respect to the environment.
Last month the UP Catalyst team visited the Innovative Product Development Unit of Riga Technical University, where the designs and construction of the pilot shipping container are conducted in collaboration with RISE. In the production system, they have designed, every step of the production including scrapping off the material and the maintenance of the container will be performed automatically, improving production efficiency.

In the meantime, our academic partner UNIBO has received the UP Catalyst samples of the CO2-derived carbon materials and performed initial tests including elemental characterization, Raman imaging, and XRD diffraction analysis to characterise the materials. The focus of the research is the performance of the material in semi-solid lithium metal batteries. A follow-up series of R&D tests are expected to occur, once the new samples are sent to battery end-user partners in the project, Bettery and UniverCell.
The ultimate goal is to build full battery cells incorporating sustainable carbon, which will be tested with regard to their lifecycle and capacity range. The next phase in the road to sustainable carbon will see UP Catalyst design and construct a 1/20 size model of a full-scale industrial pilot reactor unit, able to absorb 38 tons of CO2 and produce 140 tons of carbon material annually.